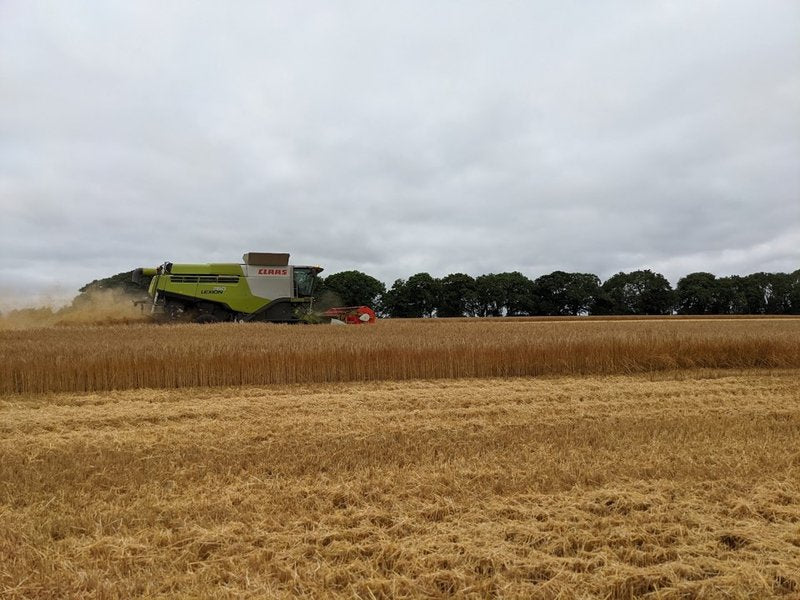
This month's Directors' Diary is all about harvest
Posted by Wold Top Brewery on
Grab a cuppa or a beer and have a read of this month's Directors' Diary - a fascinating insight into harvest...
September equals a bit of breathing space for us here at WT HQ, which is well needed.
August is a busy month. Not only do we have an influx of seaside visitors to the Yorkshire Coast who want to drink delicious beer, it’s also harvest time on the farm. The biggest event in the farming calendar.
The word ‘harvest’ comes from the Old English haerf-est which meant ‘autumn’ and/or ‘august’ and signified the period in the calendar when the crops had reached maturity and were ready to be gathered in.
The main principles behind the harvesting of grain (wheat, barley, oats etc) are threefold.
Reaping - the cutting of the grain in the field.
Threshing - separating the grain from the head of the plant.
Winnowing - removing the ‘chaff’ from the individual grains to leave it ‘clean’.
(Chaff is the lighter, outer husk of the grain and also any other straw or dust which has been mixed in with the grain.)
Pre World War 2, these three elements were all done on a manual basis. The corn would be cut, by hand using scythes, in the field and then left in ‘stooks’ to dry. These would then be collected, brought back to the farm and ‘stacked’ until the winter. Then they would be threshed (initially by hand using flails, latterly by purpose built threshing machines) to separate the grain from the straw and winnowed, using either wind or fans, to remove the chaff.
Post WW2, the combine harvester was developed, which combined (!) these three elements and enabled the harvest to be done much faster and more efficiently.
At Hunmanby Grange, Thomas Mellor (1st generation) bought our first combine harvester in 1946. It was a Massey Harris and required someone to ride alongside it to collect the grains in bags as they went along the field.
Current combines are all based on the same principle, but just have the benefits of modern technology, materials and funding!
They consist of a header, which is a series of horizontal moving blades, that cut and slice the corn. These stalks/ears of corn are then fed into the machine into a rotating threshing drum which separates the individual grains from the head of the stalk. These grains then fall through the chaffer and sieve to the collecting bin whilst the chaff and straw is sent out of the back of the machine.
Our barley, planted back in February, was harvested at the end of August. We looked for ears of corn with lots of tightly packed grains. These should be firm to the touch but not so dry and hard that they will fall from the head onto the ground below.
Farmers talk about harvest in terms of moisture and yield. Ideally, a crop of barley should be harvested at a moisture level of less than 16-18%. Most grain merchants would look to buy in grain at around 12-13% moisture which is the aim, but the British weather often means farmers have to take their opportunities where they can and then use artificial drying machines to dry the grains down once they’re brought in from the field. A harvest without having to use the dryer shed is a rare one!
Yield is the amount of grains in tonnes that the combine collects per acre. A good growing year can give yields of four to five tonnes per acre whereas a bad year might only produce yields of two to three tonnes per acre.
We’re just waiting to see what the maltsters say now!
If you enjoyed reading this and would like to sign up to our monthly email newsletter, simply follow the link http://bit.ly/WTBNews. As an added incentive, you get a discount code for 10% off your first order after signing up!
Share this post
- Tags: News